It is quite possible to repair a drill yourself if you accurately determine the cause. The apparatus often wears out bearings, rotor brushes and other mechanical elements. There may be problems with the electric motor. How to perform diagnostics at home and solve basic problems is described in this material.
The content of the article
- Main causes of malfunctions
- What is needed for diagnosis and how to conduct it
- Electrical System Repair
- Troubleshooting
Main causes of malfunctions
In order to correctly repair an electric drill, it is necessary to establish the causes of the breakdown. And for this you should familiarize yourself with its device. The device is powered by an electric motor that transmits torque to the gearbox, and then to the chuck, which firmly holds the drill. Therefore, the main risks are associated with the failure of the motor itself, the electrical system, as well as the abrasion of mechanical elements.
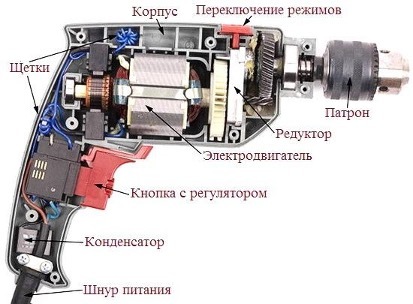
Accordingly, the main causes of malfunctions are:
- idle electric motor due to a malfunction of the stator, armature;
- problems with the brushes (wear);
- bearing failure;
- breakage of the button that regulates the speed;
- oxidation of contacts at the start button;
- breakage of the chuck that clamps the drill, due to wear of the jaws.
To carry out repairs, it is necessary to disconnect the tool from the mains and, if necessary, learn how to disassemble the drill. Further diagnostics are carried out in order to accurately determine the cause, after which they begin to eliminate the malfunction.
What is needed for diagnosis and how to conduct it
To repair a drill with your own hands, you will need the following materials and tools:
- multimeter (you can also use a voltmeter);
- apparatus for measuring short circuit in the armature;
- Screwdriver Set;
- sandpaper for cleaning contacts.
You will also need spare parts. Most often, brushes, buttons, bearings wear out. Surely the drill will need to be disassembled - then it is better to immediately replace the lubricant in the gearbox. This will reduce the load on the engine. When replacing components, it is important to use original parts. For example, if you put a regular toggle switch instead of a start button, this can lead to breakage.
To conduct a correct diagnosis, proceed as follows:
- If the drill does not turn on, the reasons may be related to the power cord. You need to disassemble the case, find the cable contacts and check them with a multimeter.
- Then they are connected to the other terminal of the cord and the plug connector. Bend the cable several times along its entire length. If the contact disappears or is completely absent, then there is a break inside the insulation. If the damage is near the edge, the cable can be cut and reconnected. But if it is in the middle, it is easier to install a new cord.
- If the cord is good, check the switch. To do this, the multimeter is connected to the terminals and tested. If the contacts are oxidized, you need to disassemble the case and clean them with sandpaper.
- It also happens that an additional contact is provided between the engine and the switch - if available, it also needs to be diagnosed.
- Check the wires, moving towards the brushes in the direction from the off button. If they work normally, it is recommended to diagnose the node. You need to make sure that the brushes are firmly pressed against the anchor, and that the carbon elements are not worn out. If necessary, replace spare parts.
- If the stator or armature windings are broken, they are replaced with new ones. In this case, you need to make several measurements of resistance. If they differ by more than 5%, the faulty windings are rewound.
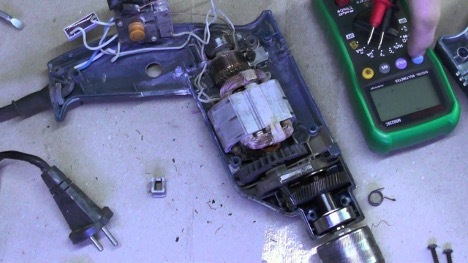
Electrical System Repair
Often it is required to repair the electric drill with your own hands, using improvised tools. Very often, the causes of breakdowns are associated with an electric motor. It is quite easy to verify this. If the cartridge turns easily, but the engine does not start, then there is definitely a problem in the electrical system. They are also indicated by malfunctions on the side of reverse rotation or speed control (number of revolutions).
During the repair, they act like this:
- If the drill does not work, the reasons may be related to the cord. It is disconnected from the network and examined with a multimeter. You can also use a battery and a light bulb assembled in one circuit. Determine the location of the break and make a repair or a complete replacement.
- If the malfunction is related to the start button, it is easier to replace it. In this case, only the original part should be used.
- It is recommended to inspect the rotor brushes as well. If they have decreased due to the erasing of the lower part by 40% or more, new ones must be installed.
- If the device does not start, and the cord is working, you need to check the capacitor for the drill. It is examined with a multimeter and, if necessary, a new one is installed.
- Next, the rotor is checked, in the presence of scale or charring, the contacts are cleaned with emery. Check the winding, rewind if necessary.
- In case of overheating, be sure to inspect the stator. Very often the varnish melts, an interturn circuit occurs. The element is checked with a multimeter, rewinded, and if necessary, a new varnish is laid.
Troubleshooting
Other ways to fix a drill involve repairing mechanical defects. If the cartridge does not scroll, but the engine is running, then there is a violation in the shaft speed. They are associated with bearings or gearboxes. You do not need to repair them - it is easier to replace them with new ones.
Often problems are associated with the cartridge. It consists of several elements, each of which can fail.
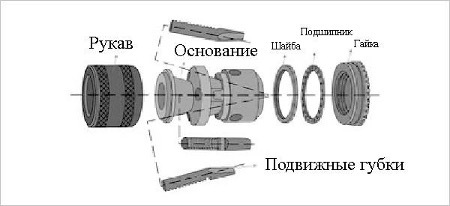
For disassembly, you can use a hammer or puncher. The latter method is more convenient - you need to act like this:
- Spread the cams so that they are completely in the body.
- A metal insert of the appropriate diameter is attached to the puncher (it should easily go into the drill chuck hole).
- Abut the cartridge against a reliable support, substituting a lining for cushioning.
- They start the puncher, after which the sleeve from the cartridge will quickly leave.
- Then the cams are removed and the mechanism is inspected. Install new parts if necessary. In this sense, the repair of a Soviet-made electric drill and modern models is no different.
Thus, the reasons why the drill does not work may be related to the electrical system or various mechanisms. Before repair, they must be accurately determined, and then replace parts or eliminate the malfunction. If you are not sure, it is better to use the after-sales service.