Argon welding is one of the types of electric arc method of joining metals. The arc is ignited in the inactive gas sphere using a tungsten electrode. At the same time, the edges of the parts to be welded are melted, reliably rallying into one.
The content of the article:
- Argon welding - features and description
- Argon welding classification
- Argon welding - what you need from tools and equipment
- Safety Compliance
- How to use argon welding step by step instructions
Argon welding - features and description
A feature characteristic of argon welding can be considered a successful combination of electric and gas welding principles. This welding technique is characterized by excellent quality welds. They are carefully polished and at the end of the entire cycle of work, the mating points are absolutely not noticeable.
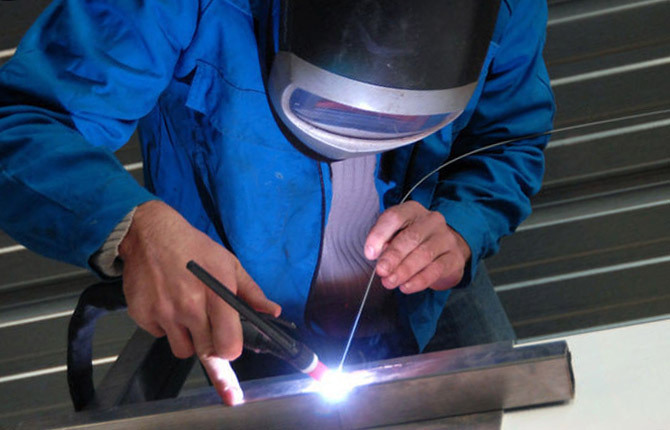
The main factor in the process is the electric arc. This is where the conversion of electrical energy into thermal energy takes place. The high thermal threshold melts the metal at the welding point. If the arc is moved smoothly, the material is fused and the workpieces are firmly connected. By moving the electrode, the parameters of the weld pool are adjusted, the welding speed, the degree of penetration, the quality and width of the seam are adjusted.
To fill the gaps, fuse a high metal bead onto the seam, a filler wire is used. It must be of the same composition as the material being welded. The filler wire is fed into the melting point manually.
The power supply is an inverter-type unit with controls, a neutral gas supply system, connectors where the burner is connected. The current can vary, be both constant and variable.
During the operation of the argon welding unit, inert argon gas is supplied through the nozzle of the tool into the arc zone. It “displaces” atmospheric air from the weld pool, including oxygen and nitrogen. Metal seams are thus reliably protected during welding. The basis of the arc is also protected - a non-consumable tungsten electrode. If, however, welding is carried out without an inert gas, tungsten is exposed to the aggressive action of oxygen and is destroyed.
Atmospheric air adversely affects the quality of the welding process.An inert gas is used to protect the fusion zone from atmospheric oxygen. In normal practice, this is argon. For this purpose, helium can be used, but its cost is much higher. The low price of argon is explained by the fact that it is just a by-product of the industrial air separation process into oxygen and nitrogen.
Advantages of argon arc welding:
- Aesthetic, high-strength seam.
- Fluxes, electrode coverings are not required.
- Work with parts of any size.
- The possibility of surfacing metal on damaged parts of parts for their restoration.
- Connection of metals that are difficult to weld (titanium, cast iron, aluminum and others).
- Minimum of emitted aerosols, in comparison with other types of welding.
- The edge of the metal cut “in argon” has an ideal geometry; oxide and nitride films do not form on it.
- The argon method allows you to connect thin layers of metal, perform special welding operations.
The disadvantages include the fact that argon metal welding is slower than it happens with other welding machines and methods.
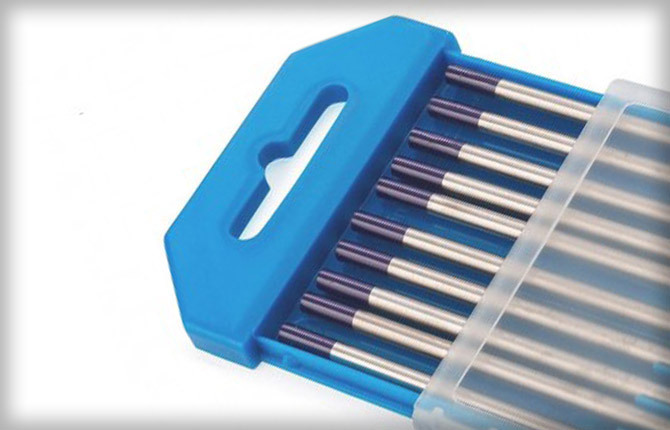
Working with argon poses a risk to human health. Inhaled argon gas provokes dizziness, can lead to nausea, vomiting, loss of consciousness and even death. Those working with argon welding often experience headaches, ringing in the ears, fatigue, digestive disorders, and breathing problems.
The welder runs the risk of getting sick with aluminosis, an irreversible pulmonary pathology, as he is exposed to the negative effects of ozone, radioactivity, and nitrogen oxides.
Argon welding classification
Argon welding technology is classified according to separate functional principles:
- Manual way. Manipulations of the torch, arc torch, filler are performed manually by the welder. His experience and qualification set the pace of the process, the parameters of the welds.
- Semi-automatic.The equipment has a function for feeding filler wire. The unit is equipped with a wire feed mechanism. The welder operates only with an argon torch, one hand remains free. It can hold or unfold workpieces. The method is more productive than manual, but the qualification of the welder is very important.
- Auto. Wire feeding, moving of the carriage with a torch takes place automatically, without participation of the worker. Benefits in smooth, high quality welds. The functions of the operator are to control and correctly set parameters - the depth of the required penetration, the optimal speed of the carriage, etc.
In addition, argon welding is distinguished by the actual process - whether a filler wire is used or not.
Without an additive, thin metal (up to 2 mm) can be welded, with a tight clamp - there should be no gaps along the seam. Then the edges melt with the electrode and this metal is enough to connect the workpieces. It turns out tight, thin, smooth, like a mirror, a seam without "scales".
With filler wire, it takes longer to cook. The type of seam is “scaly”, while the number of layers of scales directly depends on the rhythm of the additive supply to the weld pool. Qualitatively, gaps and gaps between parts up to 5 mm wide are melted, bulges are welded under the groove. The filler method is used for argon welding of metals with a thickness of 3 mm.
Not so long ago, another innovative technology of argon-arc welding appeared - robotic. Its peculiarity is that welding of parts on conveyors is performed by robotic complexes. The method is characterized by high productivity at low cost of work.
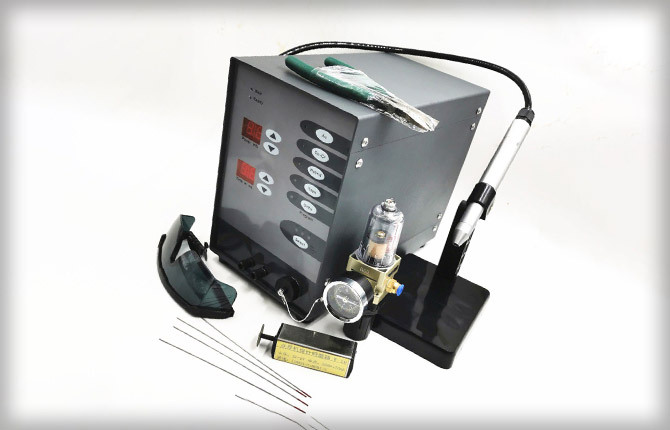
The disadvantage is the significant cost of unique equipment, the urgent need to attract highly qualified specialists for maintenance, software support, fine tuning robot nodes. The technology is designed for large volumes of production.
Argon welding - what you need from tools and equipment
Equipment and tooling for argon arc welding is divided into 3 groups.
The first one includes special devices that perform one specific operation. Argon welding, carried out by such devices, is used at large enterprises of large-scale in-line production.

Second - specialized equipment that is configured for operations with a narrow range of parts, of a certain category.
Third- universal machines, used for several types of operations and materials. This is the most popular group of mass-produced devices. They are widely used not only for industrial purposes, but are in great demand among artisanal, "garage" craftsmen.
A set of equipment for universal argon welding:
- overalls, footwear, personal protective equipment;
- unit for performing work with a non-consumable electrode;
- tungsten non-consumable electrodes;
- filler wire;
- high pressure hoses;
- gas cylinder;
- gas reducer;
- auxiliary tool.
In a gas cylinder, in a compressed form, there is a gas - argon. Cylinders are used for various gases. In order not to confuse the same container with different contents, the cylinders are marked. So raw argon is pumped into a black cylinder with a white inscription, a white stripe. Argon technical - also in a black cylinder, but the inscription is blue, the stripe is blue. Pure argon is distinguished by a gray cylinder with a green inscription and a stripe. Other special technical information is also stamped on the cylinders.
Each reducer is provided for "its" gas. The color of the reducer must match the color of the gas bottle. In a cheap version, you can use a "black", carbon dioxide gearbox. But most often a reducer with a rotameter is installed under argon.
For argon, high pressure oxygen hoses are used because of their quality and reliability. The inner diameter varies from 9 to 18 mm. So picking the right one won't be difficult.
The power source for argon welding is selected according to the goals and tasks that need to be performed during the work.

Tungsten electrodes are designed to start and maintain the arc. They have a corresponding marking that characterizes their properties, the presence of special impurities.
Auxiliary materials are needed to prepare the metal for welding, for example, a grinder, various brushes for metal.
Safety Compliance
Argon, like any other welding method, requires strict adherence to safety regulations. Most of them are simple, but their implementation allows you to save not only health, but also life.
Work must be organized in special rooms or booths. Where it is not possible to realize these conditions, the place of argon welding is fenced off with screens. They are panels made of plywood, painted with a flame retardant composition, which also includes zinc oxide, which absorbs ultraviolet rays. The height of such a fence may not be less than 2 m.
Welding argon equipment is installed on a flat area in compliance with technological dimensions. The workplace of the welder must be equipped with exhaust and supply ventilation. Exhaust panels are very effective. They are located horizontally or at an angle so that contaminated air from the arc is pumped down or away from the welder. This prevents the ingress of harmful substances into the respiratory tract of the worker.
What you need to do before starting work:
- Inspect and make sure that the special clothing, footwear, protective equipment of the welder is in good condition, clean, not saturated with oil or other combustible substances.
- Putting on overalls, fasten all buttons, tie ribbons, lace up shoes.
- The jacket and trousers are worn loose, the pockets must be closed with valves, the hair is tucked under the headdress.
- Check the workplace, lighting, hood.
- Remove unnecessary workpieces, unnecessary items, flammable materials.
- Inspect equipment. It must be reliably grounded, the high voltage contacts are protected and closed, the integrity of the wires is not broken.
- Make sure that measuring and signaling devices, blocking devices of the equipment work.
- Do not start work until the identified deficiencies are completely eliminated.
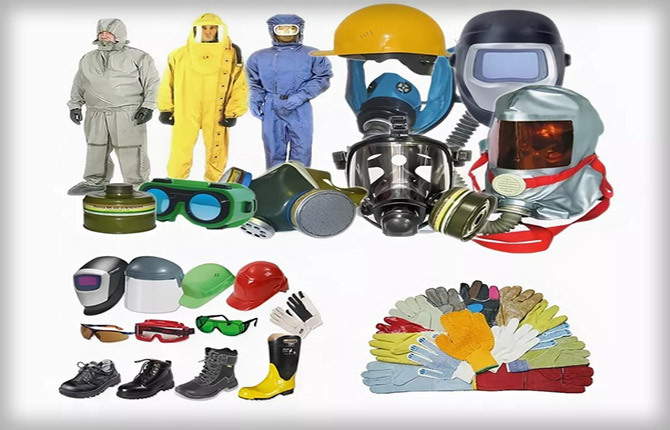
How to use argon welding step by step instructions
Before welding, the workpiece must be thoroughly cleaned of dirt, machine oil, and grease. This can be done with any solvent. When the thickness of the parts to be welded is more than 4 mm, cutting of the edges is necessary, and argon welding is performed only butt.
To destroy oxide films, the junction is treated with metal brushes. Connection with complex geometry is cleaned with an angle grinder.
To remove moisture, the workpieces should be heated to 150 degrees. Under thin metal, in order to avoid burning through, copper or steel plates are placed to remove heat.
The additive moves exclusively in front of the burner, along the welded seam.
For a short time (seconds 5-7) before igniting the arc, the inert gas supply is turned on. After the end of welding, it is again necessary to wait the same time until the gas is turned off.
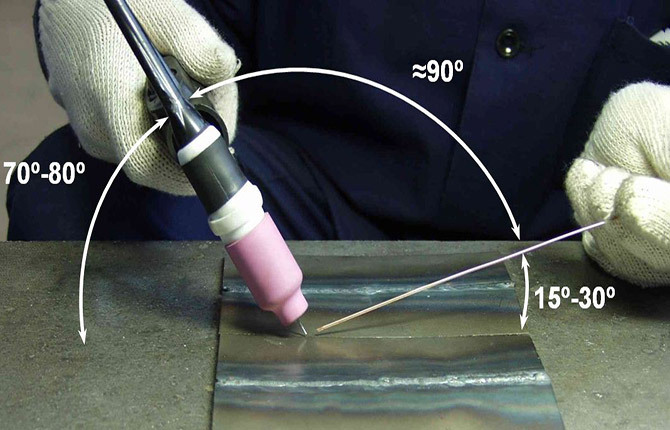
The sequence of actions for working on argon arc welding:
- Turn on equipment.
- Connect the ground wire to the welding table or workpiece.
- Open the valve on the gas cylinder.
- Bring the argon burner closer to the part to be welded so that the distance to the electrode is 3-5 mm.
- Put on a protective mask, turn on the power supply.
- Hold the resulting welding arc at the initial edge of the joint until a puddle of molten metal forms.
- With circular smooth manipulations, achieve melting of the edges of the sides.
- Keep an angle of 45 degrees between the burner and the surface.
- Slowly and carefully move the burner with the needle forward, feeding the filler wire into the torch.
- At the end of the seam, reduce the current in order to fill the crater.
Argon welding is a profitable innovative method of product restoration. The cost of welding and restoration work is much lower than the manufacture of a new part. A refurbished product can last a very long time.
Have you ever used argon welding yourself? Tell us about the characteristic features that will allow you to quickly acquire skills. Leave your comment, share the article on social networks, bookmark it.