Welding work is a complex, labor-intensive process that requires from the performer not only theoretical knowledge, but also experience and practical skills. Along with this, there is a high probability of injury. Therefore, safety precautions during gas welding are necessary to preserve the life and health of the welder and the people around him.
The content of the article:
- Necessary protective equipment
- Storage conditions for equipment and consumables
- Preparing equipment for operation
- Rules for welding work
- During welding work, it is strictly prohibited
- Welding completion procedure
- Emergency welding work
Necessary protective equipment
Safety is a type of activity that includes a number of organizational and technical measures, protective methods and means to ensure safety in production activities worker.
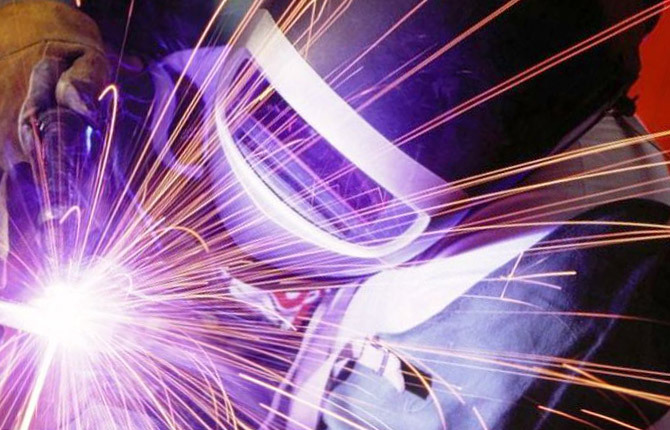
The gas welding process is a set of works using special equipment to create a strong connection between metals. According to safety precautions, there is a list of methods necessary for individual protection of eyes from radiation, skin from sparks and splashes of molten metal. In this regard, IZ means include:
- glasses, shields;
- masks, respirators, filtering gas masks;
- overalls;
- mittens - cuffs;
- leather boots with a protective toe cap.
According to safety regulations for gas welding, a protective welding shield is used, equipped with an automatic darkening filter. Glasses that do not transmit ultraviolet and infrared rays. Protecting the upper respiratory tract and lungs from smoke is a mandatory safety requirement, which is especially important in closed spaces.
Safety precautions stipulate that a welder's suit is a jacket with a secret fastener and trousers made of cotton-linen fiber with fire-resistant impregnation (canvas, tarpaulin). An option could be an apron and sleeves. A shockproof mask (electric), a protective visor made of denim, and a fire-resistant helmet are used as headgear, especially for ceiling gas welding.
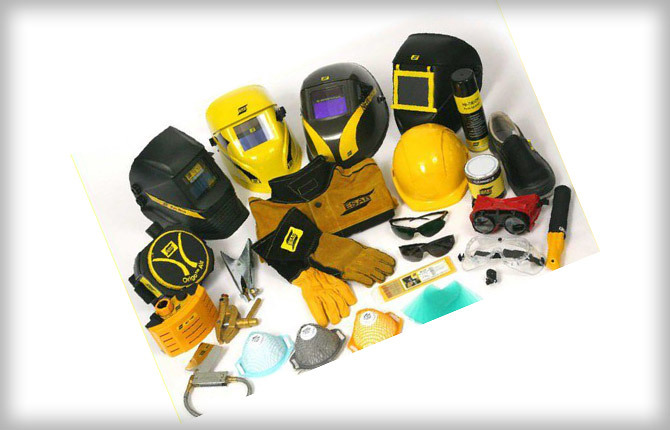
Storage conditions for equipment and consumables
The principle of gas welding is a flame that heats the edges of the workpieces, part of the filler rod (electrode), forming a welding “pool”. An open flame melts the metal edge, displaces air from the “bath”, and protects the contacts from oxygen and oxidation.
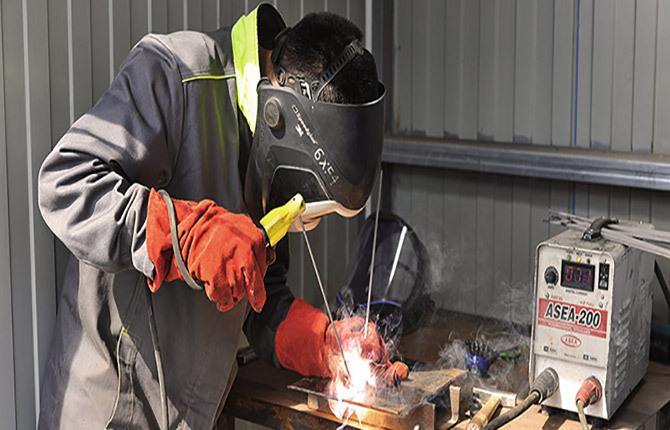
In electric arc welding, metal edges melt under high temperatures. To do this, current (alternating or direct) is supplied to the part and the electrode from the inverter. This contributes to the appearance of the arc and its combustion.
The role of the protective medium is played by the inert gas argon. It prevents air from entering the welding zone, preventing metal oxidation. Argon welding is one of the most accurate and high-quality methods. It allows you to connect parts, not only small, but also large, while observing safety precautions.
A set of equipment for gas welding includes a generator or a propane/butane cylinder. Safety water valves, which are installed on the pipeline of acetylene generators, reducers for gas cylinders, as well as high-pressure hoses, cutters, torches, electrodes, wire, flux (substances of organic and inorganic origin intended to remove oxides from welded surfaces).
Safety precautions during gas welding directly depend on the conditions in which equipment and consumables are stored.
According to safety regulations, the warehouse must be protected from precipitation, heated in the cold season, and have good lighting, ventilation system, devices that eliminate harmful gases, fumes, temperature of at least 15° with humidity up to 40%. The room should not be dusty, since the design of modern welding machines contains electronic elements: microcircuits, transistors. The floor surface is smooth and not slippery.
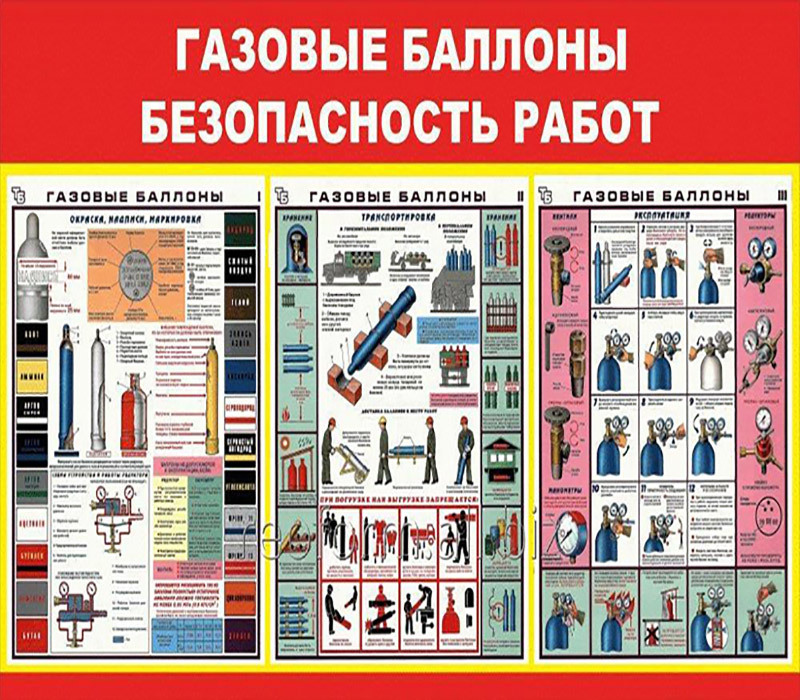
Electrodes are transported in accordance with safety regulations, in closed packaging that protects them from water, dirt, and dust. Fluxes - in containers, bags. Materials are stored on shelves indicating the type, date of manufacture, and batch number. Drying them requires a special oven, and also requires machines for cleaning and winding wire. At the welder’s workplace, stands with fastenings for cooling torches and cutters must be installed.
Full cylinders, without shoes, are placed on shelves in a horizontal position, with a stand - in a vertical position. To prevent them from falling, nests with barriers or cages are made for them.
We also read: Cold welding.
Preparing equipment for operation
For gas welding, you need two cylinders: with acetylene and oxygen. They are radically different from each other. Oxygen - blue, with a brass valve, since brass, in comparison with steel, does not oxidize. The acetylene cylinder is white, with a steel valve, and the butane cylinder is red.
You should first carefully check the equipment, first of all, the integrity of the power and grounding cables, the gas supply system, as well as the torch and its connection to the welding machine. These are the basic safety requirements.
First you need to remove the air that remains in the hose. To do this, the valves of the cylinders are opened in turn for a few seconds, then closed. Otherwise, remaining air in the acetylene hose may cause backfire (burning in the opposite direction).
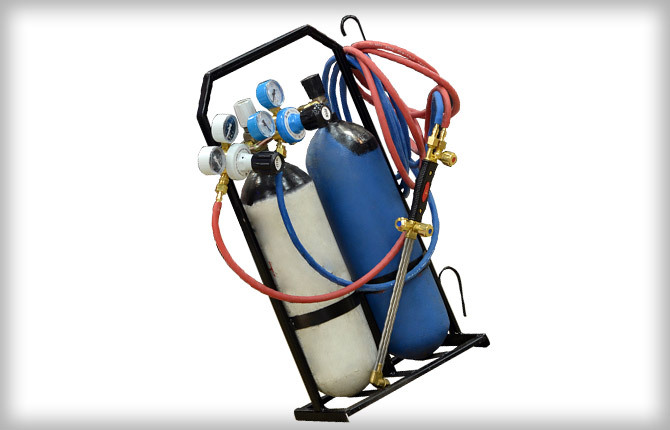
The oxygen hose is connected to the burner, and it is checked for the presence of vacuum in the acetylene tube. Next, connect the acetylene hose, tighten the clamps on both - the equipment is ready to ignite the burner. As for preparing parts for gas welding, it consists of the following steps:
- cleaning from dirt, dust, oil films;
- removal of paintwork;
- treatment against rust and scale.
Cleaning is carried out until shiny, using a wire brush or sandpaper. Aluminum is treated with an acid-based paste. Next, the welded edges are cut, in accordance with the type of connection, manually with a chisel, on a milling or special edge-planing machine. Before gas welding, the parts are tacked so that the metal structures do not change their position.
Rules for welding work
Safety precautions when working with welding require instruction. Such a program is developed by specialists in accordance with labor protection rules and approved by the manager and person responsible for safety. Depending on the purpose, frequency of delivery, and knowledge gained, the following types of instruction are distinguished:
- introductory;
- primary;
- repeated;
- unscheduled;
- target.
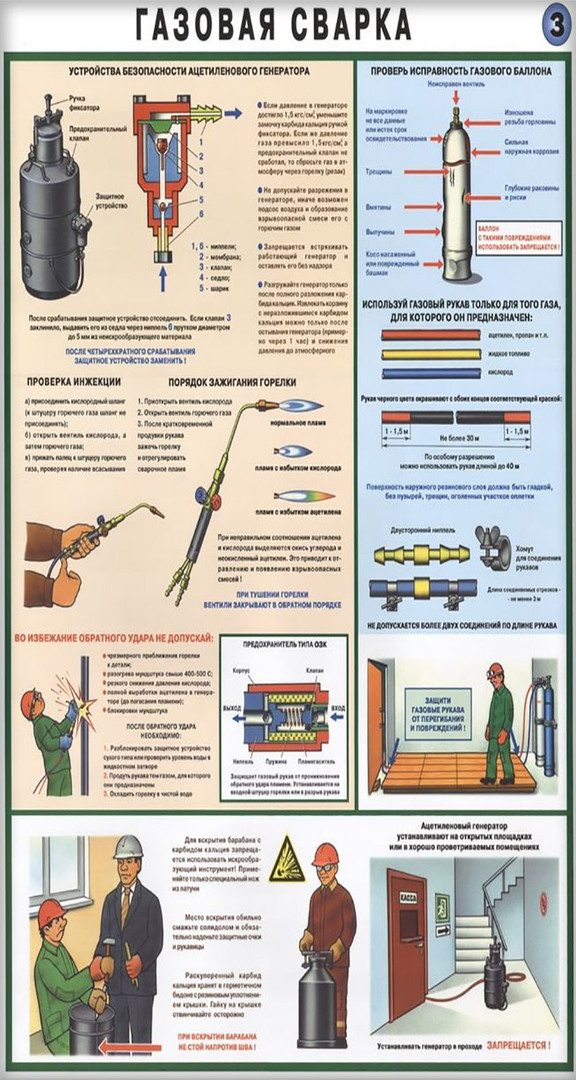
Based on safety regulations, gas welding can be carried out by organizations or entrepreneurs certified to use welding technologies at hazardous facilities. Before you start you need:
- clear the workplace of debris and flammable objects;
- protect the work area with a protection 1.8 meters high;
- check the serviceability of equipment: gas cylinders, instrumentation;
- tightness of connections, starting from the cylinder and ending with the burner or cutter;
- availability and serviceability of fire extinguishing equipment.
The place for gas welding must be provided with a fire extinguisher, a box of sand, and a shovel. Welding is prohibited when the wind speed is more than 10 m per second, at night and during a thunderstorm, as well as during precipitation without shelter.
During welding work, it is strictly prohibited
Prohibited:
- place flammable and flammable objects at a distance of less than 5 m from the place where gas welding is performed;
- carry out gas welding or cutting closer than 10 meters from the gas cylinder storage;
- at heights, use a bag under the tool to collect electrode residues;
- carry out gas welding on pipelines and containers under pressure;
- According to safety regulations, you cannot use gas cylinders with a damaged casing, faulty adapters, valves, or with an expired verification period;
- during breaks or at the end of work, leave hoses, cutters, and burners unattended;
- use liquid fuel tools, including gas cutters;
- simultaneously carry out electric and gas welding on ladders and stepladders;
- work on freshly painted, flammable paints or varnishes, products;
- use IZ products with traces of oil, grease, gasoline, kerosene.
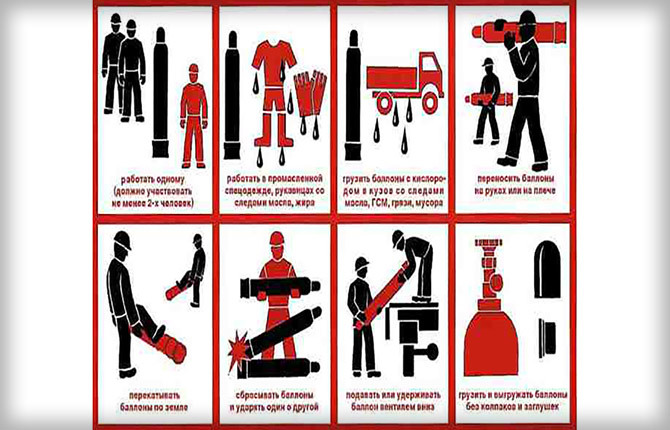
Welding completion procedure
The final technological process, tempering, is the heat treatment of the metal, keeping it below the critical temperature for a certain time, cooling to air temperature. This procedure is necessary to eliminate internal stresses that can affect the quality of the weld of a metal product.
A weld is essentially a local casting with defects that occur as the metal solidifies. Therefore, for parts with clear and defined shapes, general or local heat treatment of welds is performed. The structure of the alloy contains columnar crystals, an increased content of gases, and a layer of incomplete melting.
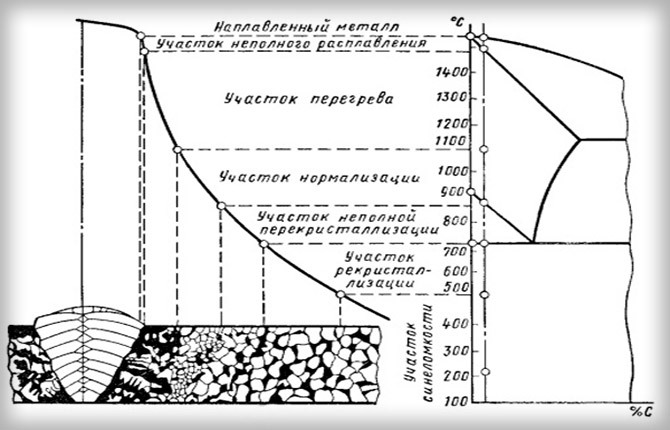
Tempering is carried out, for example, during gas welding of alloy steel products. To do this, the weld area or the entire part is completely heated with an inductor or flexible heater at a temperature of 900–950°, followed by holding and cooling. Medium and low carbon metals are heated to 650°. At such temperatures, special attention should be paid to safety precautions.
The burner flame does not perform protective and restorative functions in relation to the connected material to the fullest extent, therefore manganese and silicon are added to the additive wire for oxidation metal These substances in the molten state form slags, which protect the gas welding area from the effects of nitrogen, hydrogen, and oxygen.
Upon completion of the work, the connecting seam is covered with insulating material: fire-resistant glass wool, ceramic fiber canvas, kaolin wool.
Emergency welding work
Water pumps, heating mains, steel wells, fire-fighting tanks, housing and communal services and many other services often need repair welding work. The location of the emergency area is determined by written permission of the person responsible for safety precautions.
Their peculiarity is the difference in performance in winter, as well as strict adherence to safety precautions. It is impossible to stop welding in an emergency situation, despite the influence of negative temperatures, snowfalls, and strong winds. Shelters do not always guarantee a prepared place from rain and snow. Even a small amount of moisture affects the quality of the seam.
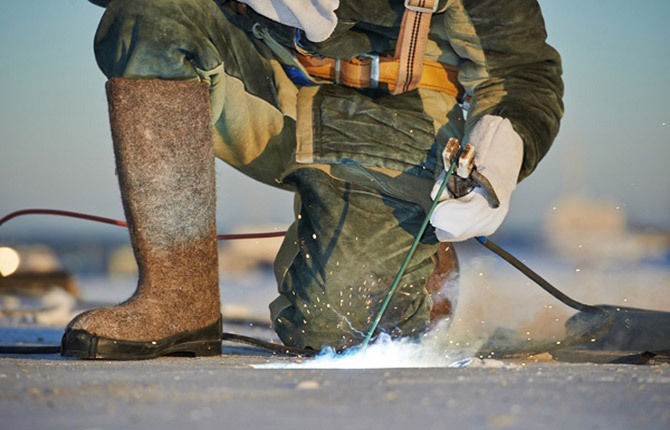
Under the influence of a flame, water decomposes into hydrogen and oxygen. Hydrogen reacts with the metal, resulting in a poor-quality compound. To eliminate moisture, dry and warm up the welding site using a hygroscopic substance, Portland cement, which absorbs water vapor. In emergency situations, strict adherence to safety precautions is especially necessary.
The main positive feature of gas welding is autonomy. With this method of connecting parts, it is easy to change the heating level and the degree of metal melting. To do this, it is enough to reduce or increase the distance of the torch to the materials being joined, or change the angle of inclination. It is important to remember safety precautions. Disadvantages include low productivity and the need to find an experienced welder.
What do you know about new welding methods? Leave your comment on the article, share it on social networks, bookmark it.
When oxygen and gas are closed, a bang occurs, this is alarming, what is the reason and how to avoid it?
The popping noise usually occurs due to combustion moving inside the burner mouthpiece, which is actually a backfire. This happens when the flow rate of a mixture of oxygen and combustible gas becomes less than the speed of propagation of the combustion front. When turning off the burner, it is correct to first turn off the flammable gas, then the oxygen - in this case there will be no popping noises.