The most common type of welding is spot welding. It is used to connect metal parts and structures. The quality of such a connection will depend on the correct duration of the electrical pulse. Let's look at how to make spot welding.

The content of the article:
-
Preparing for spot welding
- Preparing the welding machine
- Preparation of welding electrodes
- Surface preparation
-
Spot welding technique
- Selecting a welding location
- Spot welding application
-
Features of spot welding
- Advantages and disadvantages
- Areas of use
-
Basic mistakes when spot welding
- Description of errors
- Ways to fix them
Preparing for spot welding
To make a high-quality connection, it is necessary to carry out the preparatory work correctly. They consist of preparing the surface, welding machine And electrodes.
Preparing the welding machine
To carry out welding, special equipment is required. Enterprises use welding machines. They are able to work with different types of metal.
Household consumers use compact welding machines. The device comes with clamps and a low-power transformer. Before putting it into operation, it is necessary to check the correspondence of the power of the welding machine and the power supply indicators.
After this, the welding wire is installed. Its type and diameter must correspond to the tip of the welding gun and the guide hose. If you need to use a wire of a different diameter, the drive roller is turned over or replaced with a suitable one.
The welding machine spool can have different sizes. If it does not fit, use an adapter. Before starting the adjustment, the wire is installed in the desired groove. After this, it is pressed with an adjusting roller.
At the next stage, the supply hose is prepared. It needs to be unfolded, eliminating kinks. This can be done conveniently on a flat surface.
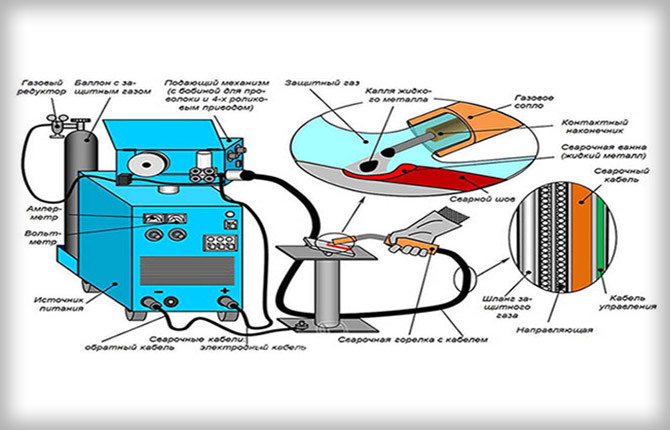
We read: Electric welding for beginners
Preparation of welding electrodes
An electrode is the main attribute of welding, which performs the function of supplying electric current to the parts that need to be welded. For their manufacture, alloys with high electrical and thermal conductivity are used. Copper or bronze alloys have these qualities.
The tip of the electrode heats up the most, so this is the part that most quickly becomes unusable. Because of this, it needs to be sharpened during welding work. The optimal tip shape is a cone.
To extend the use of electrodes, a number of conditions must be met:
- choose an electrode based on the material you need to work with;
- use a water jacket;
- Do not use thin-tip electrodes for heavy welding;
- Store the electrodes correctly and prevent them from being damaged.
Preparing electrodes for work involves calcining or drying them. This must be done to reduce the level of moisture in the coating, which adversely affects the quality of the work performed.
Undried electrodes are difficult to ignite, crumble or stick. Drying must be done immediately before using them, since calcining the same electrode more than 3 times can lead to the coating coming off the rod.
Surface preparation
Before carrying out spot welding with your own hands, you need to prepare the metal. The process consists of cleaning the area where the seam will be made from corrosion, contamination, and oxidation. Without this, during operation, the power of the device may decrease, and the degree of its wear increases.
To clean the surface, use a grinder with sandpaper, a metal brush or sandblast. If the part is small in size, it can be kept in a special solution.
The preparation process will be different when working with aluminum or an alloy made from it. There is an oxide film on the surface of this metal. It does not allow the part to be fully heated and welded. Therefore, it must be removed before starting work.
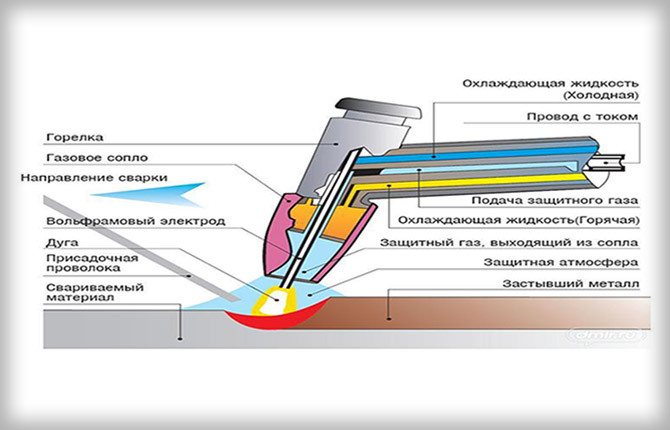
Spot welding technique
The spot welding process is based on a pulse of welding current, which leads to heating of the parts. Its duration is 0.01-0.1 s. Such a pulse leads to the melting of the metal in the contact zone with the formation of a liquid core. It will be the same for the two parts that need to be assembled. After this, the parts are held for some time until they cool and the core crystallizes.
Selecting a welding location
The place where welding work is carried out must be kept clean. All tools must be in good working order. Work on fastening or assembling structures must be carried out in trestles, on a flat surface.
The transformer is placed on a metal platform with a height of 10 and a width of at least 80 cm. Access to them must be free. Switches for the transformer are placed on tubular stands. Current converters are mounted on the floor next to the columns, and switching devices are mounted on the wall of the column.
For safe welding work, stable ventilation is required. This will reduce the amount of harmful substances that appear in the air during spot or other welding.
We read: How to weld vertical and horizontal seams using electric welding
Spot welding application
There are several stages of the spot welding process:
- surface cleaning, leveling and fitting of workpieces;
- fixing parts with pliers with compression to a slight deflection;
- heating the metal using an electrode, melting it, forming a welded core;
- when working with an automatic device, compression is released;
- turning off the current after the working surface acquires a red tint;
- strong compression of parts to form a high-quality welded core when the metal cools.
To prevent metal spattering, it is necessary to control the compression of parts during the application of current.
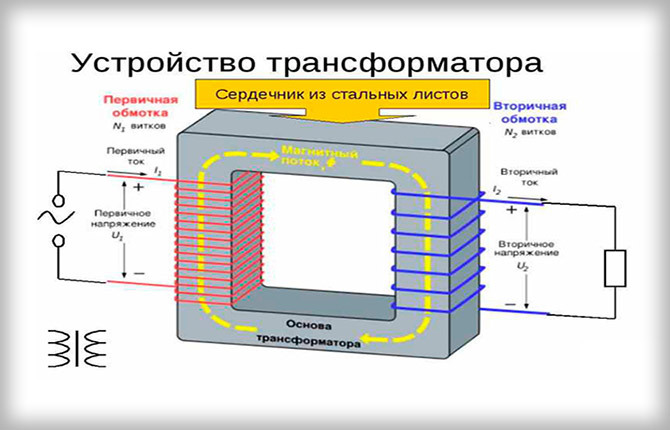
Features of spot welding
A special feature of the point method is the clamping of parts with special pliers through which an electric current is passed. With its help, the metal at the point of contact with the electrode is heated. At this time, the part is compressed and in some softened areas a kind of “hot rivet” is obtained, limited by a point.
Features of spot welding:
- operating voltage - less than 10 V;
- operating current - over 1000 A;
- short-term connection (a few seconds);
- high pressure created by pincers.
Advantages and disadvantages
Advantages of the spot method of welding metal elements:
- High speed. High temperature promotes rapid and uniform joining of metal. This avoids its deformation.
- Low costs, allowing point technology to be used en masse. Automating the process further reduces costs.
- Low energy consumption compared to other welding techniques.
- Ease of doing the job.
But the technique also has disadvantages:
- Inability to connect parts of large thickness. This is due to the fact that the resulting seam will not be strong enough and may be damaged as a result of physical or mechanical impact on the part.
- Welding work requires free space.
- The appearance of the connection may not be attractive enough, so the point technique is used in inconspicuous places.
- High danger during work. It is important to follow safety precautions to avoid injury. Special protection against metal splashes and sparks is also required.
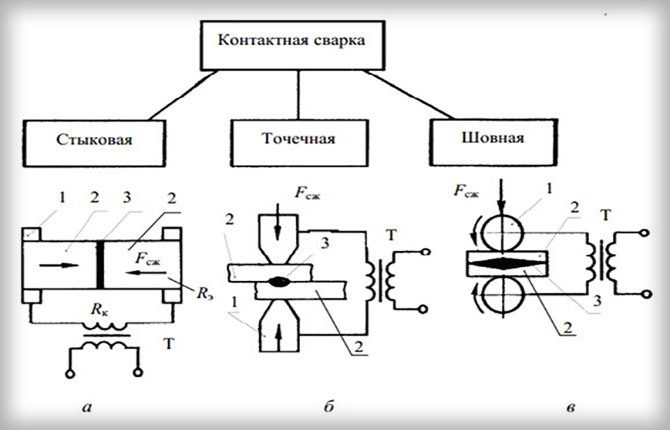
Areas of use
The spot welding method is used when it is necessary to make metal structures by connecting individual elements. The technology is reliable, fast and easy to perform, and the process itself can be automated. Therefore, the technique is used if you need to make the following structures:
- automobiles, agricultural, railway and other equipment;
- household appliances (refrigerators);
- microelectronics elements;
- frames made of reinforcement for monolithic slabs;
- jewelry.
Basic mistakes when spot welding
To make a durable product, it is important to avoid common mistakes when carrying out welding work. What do you need to pay attention to in order to make a high-quality design?
Description of errors
Spot welding requires precise settings and monitoring of the results obtained. The most common mistakes made are:
- Burnout. It is a hole in the structure, the edges of which can easily come off. This occurs when there is a long pulse, high current, or great compression of the metal part, which causes it to overheat and drain. To avoid this, you need to make the pressure weaker or reduce the current.
- Spills. If a weak pulse is applied for a long time or strong compression is applied, the metal can move beyond the core with the formation of voids. During operation, such splashes resemble sparks that fly out from points. The thickness around these points is reduced, making the connection less secure.
- Lack of penetration. The core may not be heated up if you make a weak impulse, loosen the pliers and do not compress the part too much. This can lead to such a point coming off during physical activity. Lack of fusion can occur where weld points are close to each other, so the adjacent point becomes a shunt, conducting some of the electrical energy. It will not be enough to melt the metal.
- Reducing the diameter of the point. If you make a short pulse or press the parts loosely, the melt area will be insufficient. In this case, microalloys are formed at the point, which are weaker than monolithic welding.
- Cracks in metal. They can appear if the points are made near the edge of the overlap, the metal is not prepared, or the pliers are not properly compressed. Such a defect can be examined under a magnifying glass.
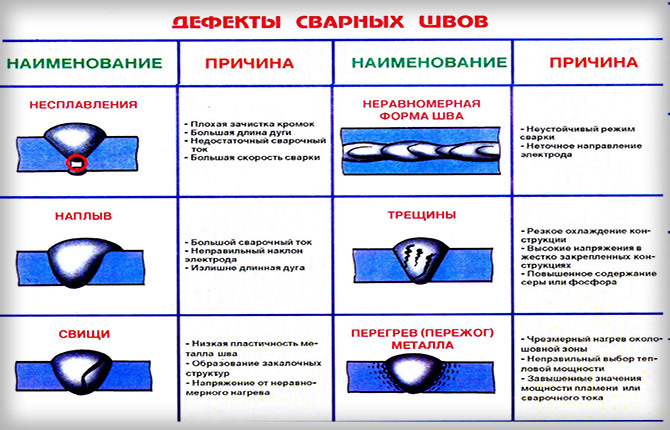
Ways to fix them
Checking the quality of spot welding is quite difficult. Ultrasonic techniques commonly used in manufacturing may not be effective. To check the finished part, a control fracture test is performed.
If defects are identified, you can do the following:
- re-weld the point;
- clean up external splashes;
- drill out the defect and re-weld it using a semi-automatic welding machine;
- make a rivet (blow or welded);
- forge the hot spot.
Spot welding technology is quite common. But professional equipment is expensive, so craftsmen at home can make homemade devices from old microwaves. Drawings and diagrams of the device are available on the Internet.
Spot welding is easy to perform and has minimal financial costs. When performing it, it is necessary to observe safety precautions and adhere to the rules of work. This will reduce the risk of injury and allow you to make a high-quality metal structure.
Do you have spot welding skills? Share your secrets in the comments. Also don't forget to bookmark the article and share the link with your friends.